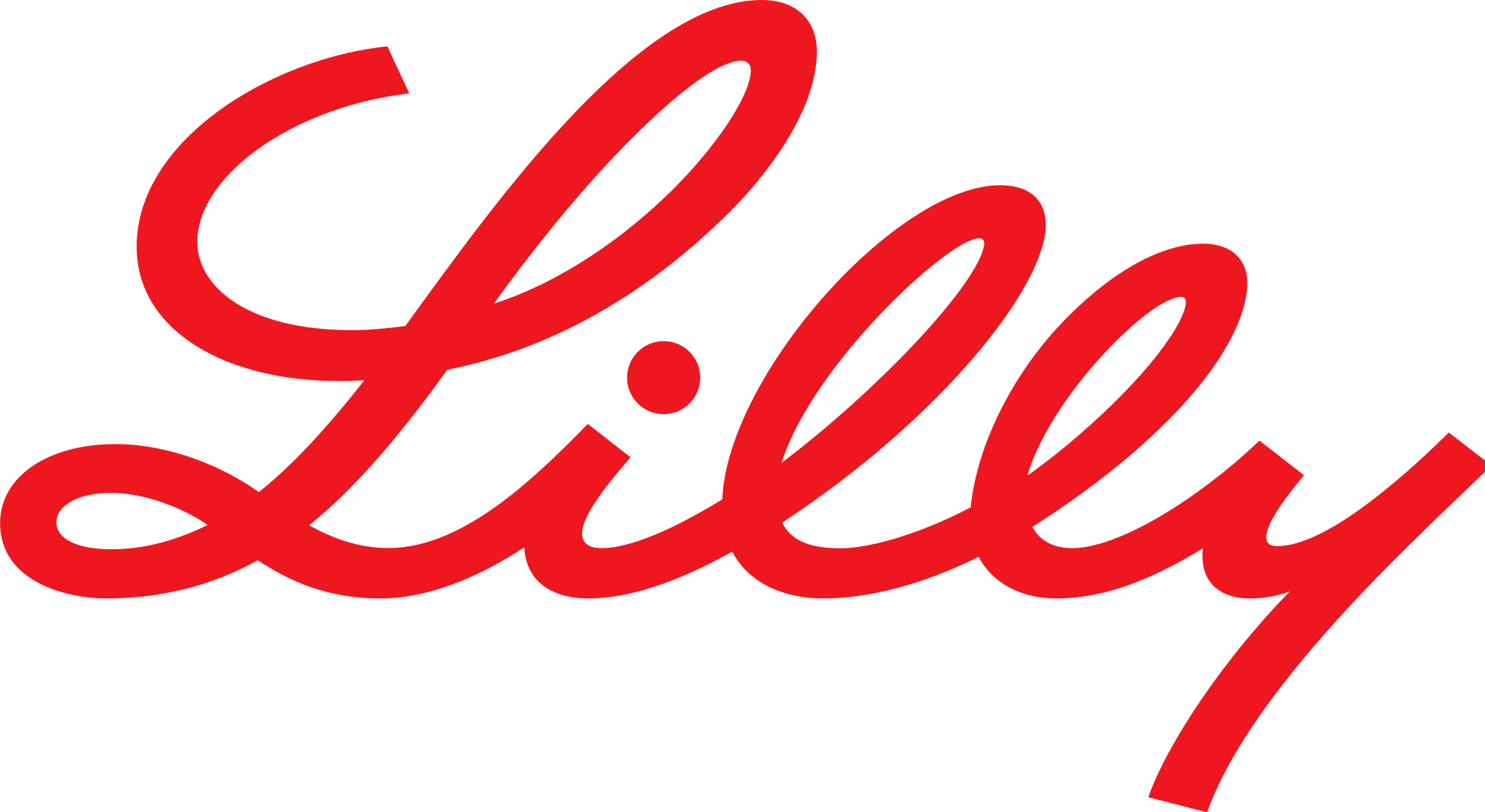
Principal Maintenance Engineer – Maintenance Engineer
Eli Lilly
- Limerick
- Permanent
- Full-time
- Have a good understanding of the site’s production infrastructure. This includes, electrical, Mechanical & E&I systems, steam, process water, life safety, and the criticality of their use/or function.
- Assure that maintenance and related infrastructure are “fit for use” when needed and in a state of compliance.
- Maintenance of electrical / mechanical systems of the manufacturing plant, from installation to troubleshooting.
- You are called upon to improve the plant's efficiency, upgrade to new technologies, repair equipment, increase production, and reduce manufacturing issues including bottlenecks.
- Understand the design history of the plant/facility (including Code, Environmental and/or other regulatory limitations, which may exist).
- Have a basic understanding of the customer processes supported (e.g., manufacturing, laboratory, admin) and understand day-to-day issues of the actual operation.
- Work directly with Utilities, Automation and Operations personnel to identify and develop the Plan for asset recapitalization. This information should be used as input for completing the annual Resource Assessment (RA).
- Provide engineering expertise to the Maintenance Department and the maintenance principal engineers (Mec, Elec, E&I) in the evaluation of Maintenance Strategies.
- Should have a basic understanding of the tools for condition-based maintenance.
- Understand and apply engineering, quality, and health, safety and environmental requirements and practices as defined in Lilly Global Engineering Standards and Best Practices, Global Quality Standards and HSE Standards.
- Know what jurisdictional codes apply and work to achieve ongoing compliance.
- Know, understand, and apply the appropriate level of Root Cause Failure Analysis to determine the cause and develop the countermeasures to prevent the problem from reoccurring.
- Fully meet roles and responsibilities as described in the Manufacturing Standards for Operational Excellence.
- Changes in facilities are still within allowable load limits for buildings and structures.
- Building Code analysis has been performed to ensure the proposed new function meets Building, Fire, and other Codes.
- New changes are in compliance with allowable occupancy limits for rooms.
- Participate and evaluate corporate and regulated assessments or compliance requirements/initiatives providing technical support and expertise on facilities/utilities/maintenance aspects.
- Participate in long range plan development exercise to provide technical support and input for projects definition and implementation plans.
- Comply with applicable trainings as assigned.
- Participate in the training process of other employees.
- Participate in teams designated by his/her supervision (i.e., Contractor Safety, Best Management Practices (BMP).
- Support/Lead Changes and/or investigations related to his/her area of expertise.
- Develop and maintain updated the obsolete assets strategy of the Plant (a site plan drawing and written document with the list of assets not currently in use).
- Communicate effectively with key personnel from other sites and functional areas to facilitate improvements, technology transfer and troubleshooting.
- Help to identify and coordinate shutdown activities.
- Identify required actions/projects to be implemented during shutdown.
- Support mitigation strategies to avoid plant interruptions and support/develop return to service strategies.
- Review and provide feedback to Engineering Standards related to Capital Delivery.
- Participate on design review meetings related to capital projects to assure that Engineering Standards and Master Spec’s requirements are being incorporated.
- Participate and develop the annual Resource Assessment (RA) for areas of expertise or support provided.
- Support development and routine review process for t the Site Master Plan of the Site.
- Comply with procedures of Occupational Safety and Environmental groups.
- In case that the tools are not available, he/she must request them to their supervision.
- It is his/her responsibility to request the basics tools to perform their job in a safe and healthy manner (ex: equipment, trainings, etc.)
- In case of any concerns, they must immediately communicate with Occupational group (H&S).
- Identify and alert of potential risks observed in their area and notify them to their supervision.
- Immediately report any occupational incident, spill, or situation in which he/she gets involved to their supervision.
- Such communication may be written or verbal. Immediately means without delays, at the same work shift, and before leaving his/her working area.
- Report the near misses at the moment in which they occur or are identified and adequately document them, according to the available and established mechanism.
- Participate in the evaluation of incidents and near misses in his/her working area and provide suggestions to prevent future incidents.
- Evaluate his/her personal actions in order to avoid accidents.
- Shall not take any risks in regard with his/her health and safety and shall not create situations of risk that may affect other coworkers and understand that personal and coworkers’ safety cannot be impacted in anyway.
- Ensure that his/her coworkers act in a safe way and without risking his/her personal and others safety.
- Actively participate along with and help Occupational Safety in activities or initiatives to improve the area from the perspective of health and safety (e.g., Process Team, Sub-teams).
- Use the equipment provided by the company to avoid accidents and sickness (e.g., safety glasses, boots, respirators, etc.).
- Take good care of his/her personal protection equipment (safety equipment).
- Attend the health and safety trainings coordinated by the employee, his/her supervision, and the Training Department.
- Keep updated all the required licenses/certifications for the performance of his/her job.
- Never operate equipment that requires licenses/certifications if they are expired.
- Attend the appointments of medical screenings.
- Work under limited supervision in accordance with the laws, and local regulations and policies, procedures, standards, and guidelines of Lilly global.
- He/She will need to support the start of a new production facility and new site services.
- He/She will need to support the development of training material.
- Work with project team to ensure successful handover of systems from project to site.
- Development of efficient and sustainable business processes & practices.
- Develop and support digital initiatives.
- Supporting operational readiness plans and schedule adherence.
- Be flexible to support a fast-changing startup of a new facility.
- Comply with the safety goals and objectives of the organization.
- Monitor personal performance in the industrial health and safety area.
- Notify and initiate actions to correct any hazard conditions/risks in my working area.
- Actively participate in the safety trainings applicable to my area.
- Notify Management of any emergency incident, register, and comply with the communications requirement.
- Use all office supplies in an efficient manner.
- Make copies on both sides of the paper to minimize paper waste.
- Use the electronic mail system as possible to minimize paper waste.
- Turn off the lights and the equipment when not in use to save energy.
- Observe, promote, and comply with EPA and internal environmental standards as appropriate.
- Comply with Environmental Permitting requirements.
- All site departments
- Contractors
- Corporate, other Lilly affiliates, internal and external auditors, regulatory agencies, local agencies, and vendors ((e,g.OMPU, EPA, FM, FDA, etc)
- Global Lilly forum linkages related the role.
- Engineering Tech Centre
- GFD (Global Facilities Delivery)
- Work during long or short periods.
- Memorize oral and written instructions.
- Work with multiple tasks within distraction environment.
- Work under pressure.
- Realize repetitive tasks.
- Work with occasional supervision.
- Create positive interpersonal skills and relationship.
- Work during extender periods, work under pressure, and good judgement under special circumstances.
- Travel (within and outside country).
- Work as a resource in other strategic areas of business.
- Effective leadership.
- Self-starter, teamwork oriented.
- Knowledge on cGMP’s, Pharmaceutical Sciences, regulatory trainings.
- At least 5 years on pharmaceutical industry preferably with experience on Engineering, Maintenance, Utilities, Manufacturing and Facilities.
- Experience on equipment design, construction and start up.
- Excellent communication skills at all levels.
- Consistent self-initiative to resolve discrepancies.
- Excellent English.
- Excellent Technical documentation and review.
- Excellent Technical Writing skills.
- Knowledge of computerized systems, documentation of Good Manufacturing Practices, E&HS Regulations